In the highly competitive world of manufacturing, Cost Reduction has become a crucial strategy for maintaining profitability and staying ahead of the competition. Identifying and eliminating waste is a fundamental approach to achieving this, allowing businesses to streamline operations, improve efficiency, and reduce unnecessary expenses. This article explores key strategies for manufacturing cost reduction with a particular focus on waste elimination.
Cost Reduction Through Process Optimization
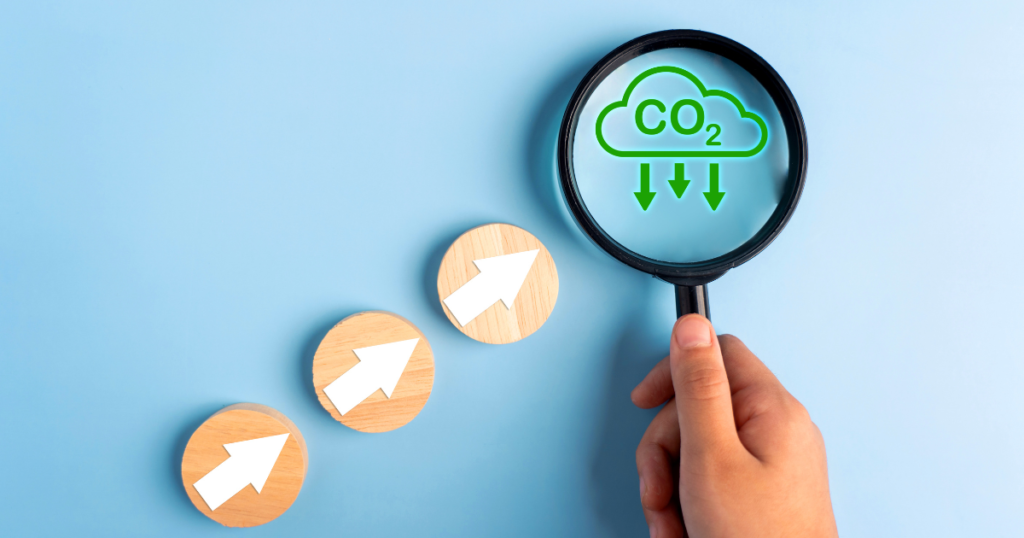
One of the primary strategies for Cost Reduction in manufacturing is process optimization. This involves analyzing every step of the manufacturing process to identify inefficiencies and areas of waste, such as excessive use of resources or time spent on non-value-added activities. By implementing lean manufacturing principles and continuous improvement practices, companies can significantly reduce waste and optimize production processes, leading to lower costs and improved productivity.
Supply Chain Management for Cost Reduction
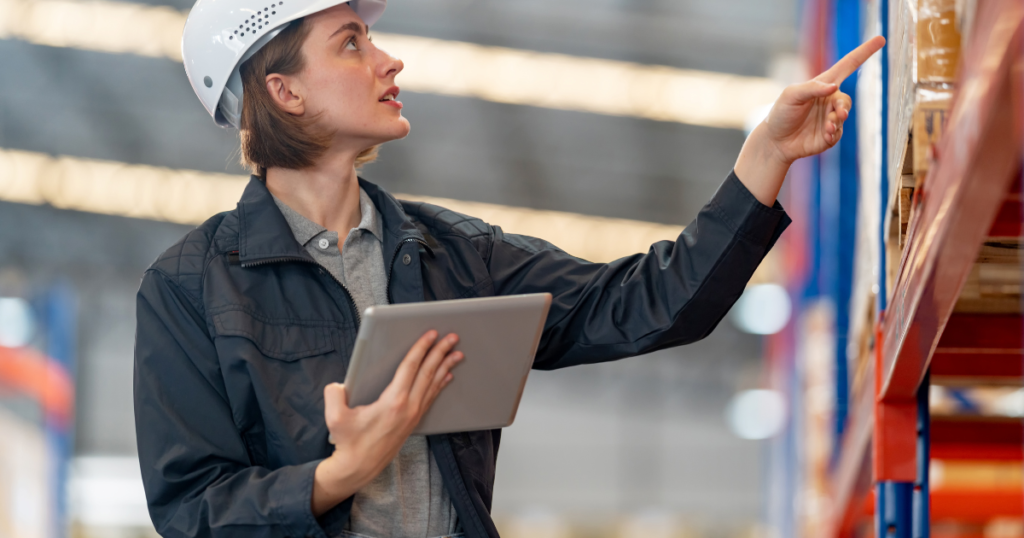
Effective supply chain management is another critical area for Cost Reduction. By closely monitoring and optimizing the supply chain, manufacturers can reduce costs associated with procurement, inventory holding, and logistics. Strategies such as just-in-time (JIT) inventory management, supplier consolidation, and strategic sourcing can help eliminate waste in the supply chain, contributing to overall cost savings.
Energy Efficiency and Sustainability
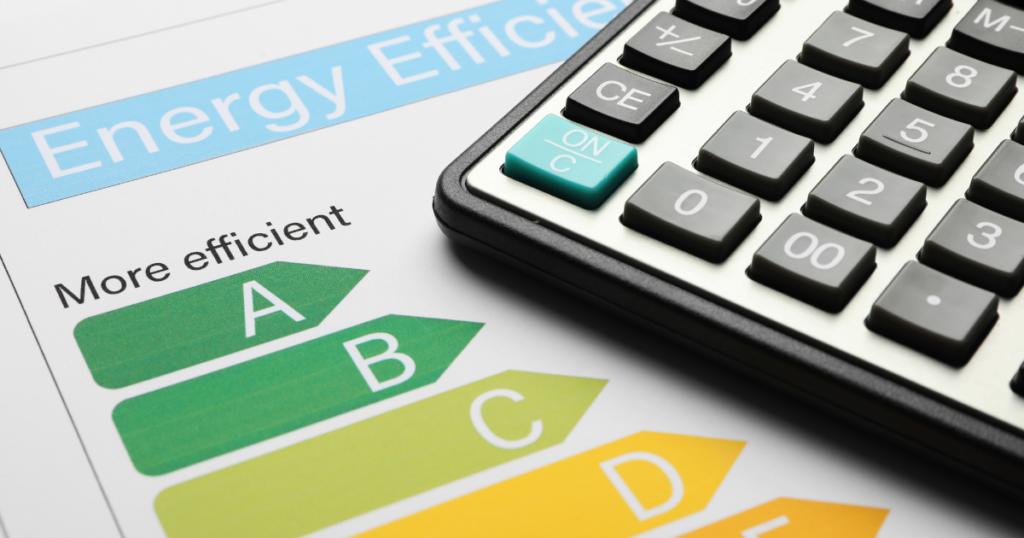
Energy consumption is a significant cost factor for manufacturers. Implementing energy efficiency measures not only reduces operational costs but also contributes to sustainability goals. Manufacturers can adopt energy-efficient technologies, improve facility insulation, and optimize equipment usage to minimize energy waste. Renewable energy sources, such as solar or wind power, can also be explored to further reduce energy costs and environmental impact.
Technology Integration and Automation
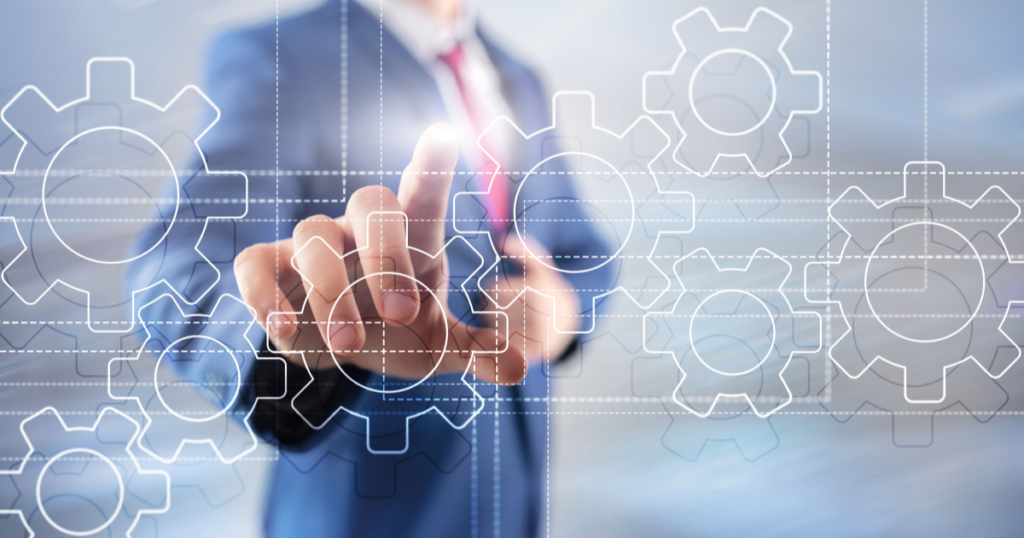
The integration of advanced technologies and automation in manufacturing processes is a powerful Cost Reduction strategy. Technologies such as the Internet of Things (IoT), artificial intelligence (AI), and robotics can streamline operations, reduce labor costs, and minimize errors and waste. Although the initial investment may be high, the long-term savings and efficiency gains can be substantial.
Employee Engagement and Training
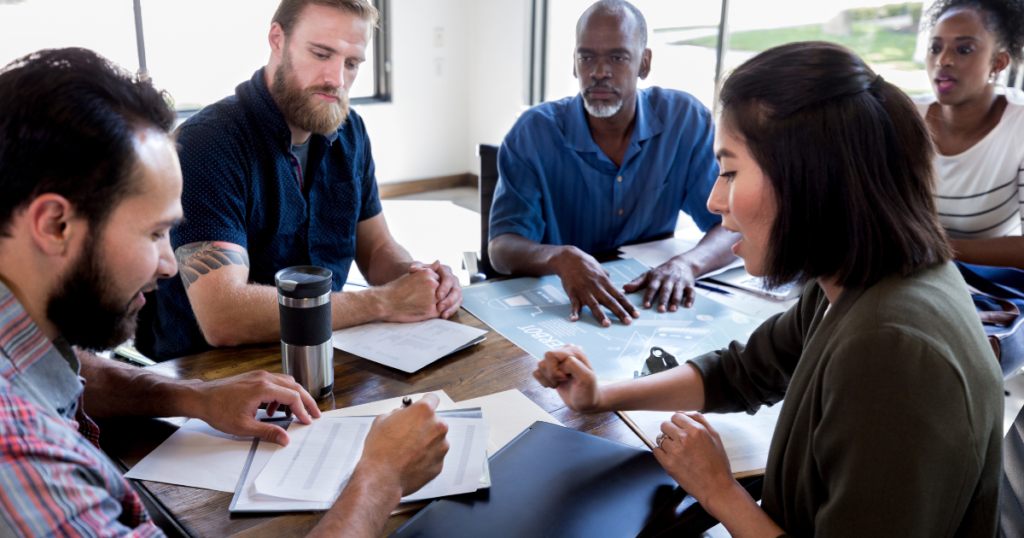
Engaging employees in cost reduction initiatives is essential for identifying and eliminating waste. Workers on the front lines are often best positioned to notice inefficiencies and propose practical solutions. Regular training and a culture that encourages continuous improvement can empower employees to contribute to cost reduction efforts, leading to a more efficient, productive, and engaged workforce.
Regular Review and Continuous Improvement
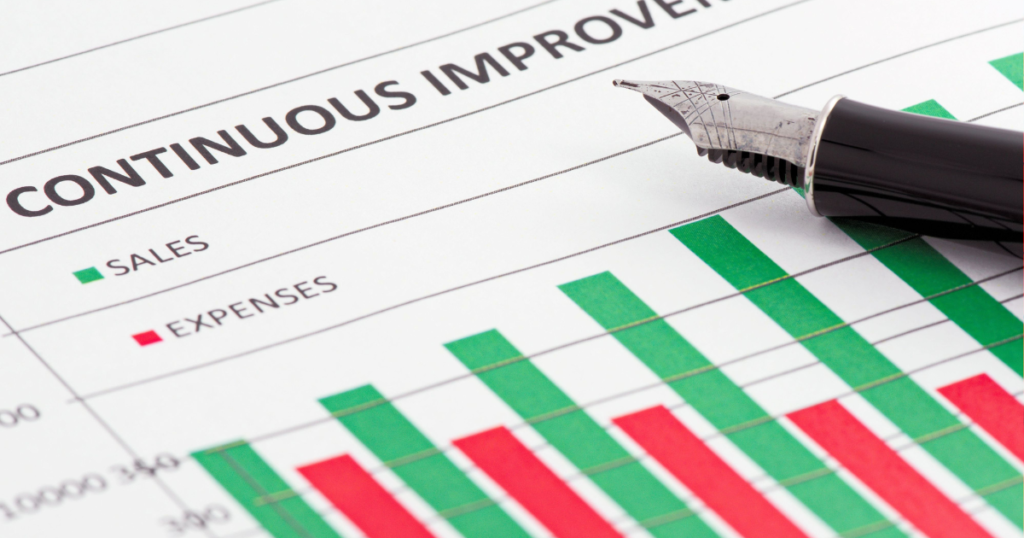
Finally, a commitment to regular review and continuous improvement is vital for sustained Cost Reduction. Manufacturing processes and market conditions are constantly evolving, making it necessary to continually assess and adjust strategies for waste elimination. Regular audits, performance metrics, and feedback mechanisms can help identify areas for improvement, ensuring that cost reduction efforts are effective and aligned with overall business objectives.
Conclusion
Cost Reduction through identifying and eliminating waste is a multifaceted strategy that requires a comprehensive approach. By focusing on process optimization, supply chain management, energy efficiency, technology integration, employee engagement, and continuous improvement, manufacturers can significantly reduce costs and enhance their competitive edge. The key to success lies in a commitment to efficiency, innovation, and a culture that values continuous improvement. With the right strategies in place, manufacturers can achieve substantial cost savings, ensuring long-term profitability and sustainability in a challenging market environment.
No responses yet